I cut Mona Lisa, on 100x100 mm aluminum plate, using my newly created program, photo2cnccut.
This is the data to cut (jpeg). I've got the picture from Wikipedia, cropped and grayscaled.
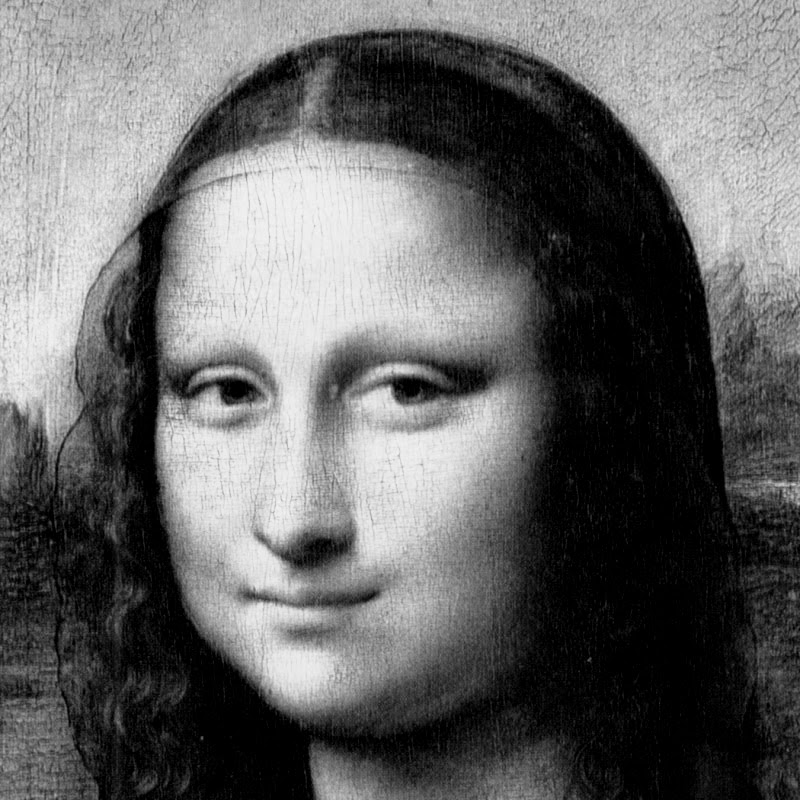
This is the program-processed cutting data (svg). The black lines are where the tool passes, with varying depths.
Since it just cuts many straight lines, the method is not so slow, relatively speaking, (30 minutes rather than 3 hours).
But as you see, by just cutting, it didn't make a great object.
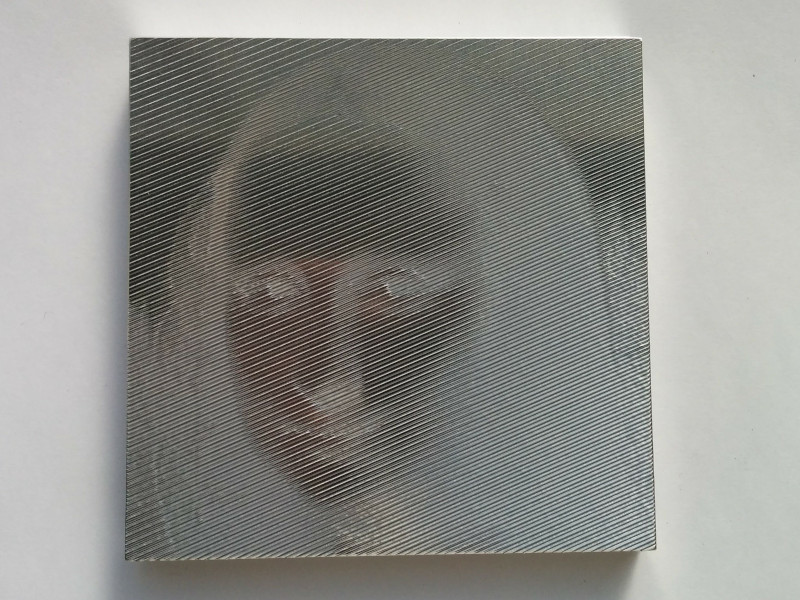
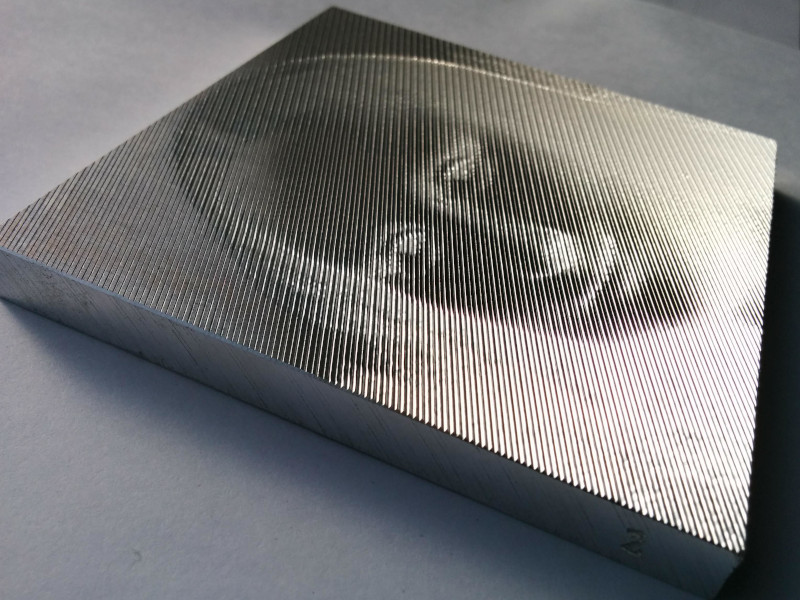
From a very narrow angle and lighting, you can discern the original picture.
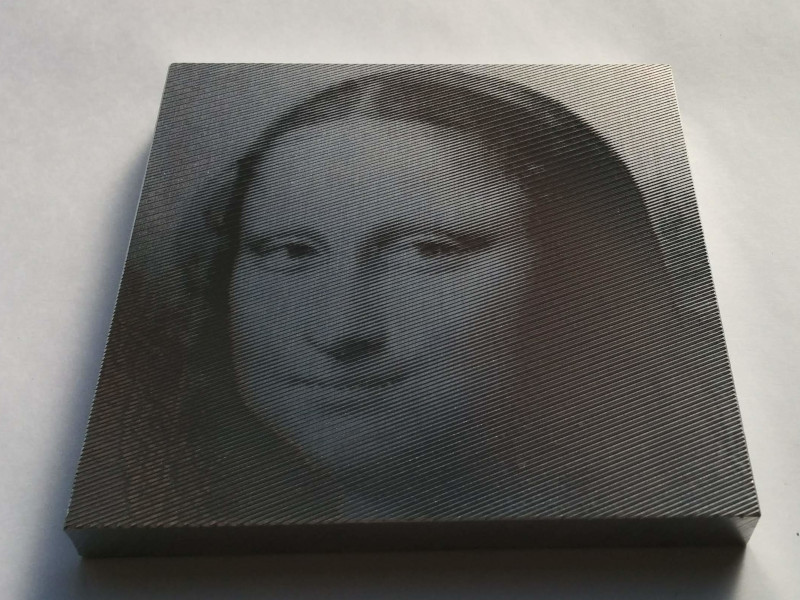
I painted the grooves (spray black paint and sand the surface). Now you can see the face from the front.

---
The method translates grayscale image intensities (0 to 255, or black to white), to g-code Z depths. So the tool tip is rather important.
The minimum diameter must be small enough.
The steeper the angle, the better the effect.
The tool tip shape should be uniform.
The cutting data was created with 0.6mm maximum width. I assumed the tool should be able to cut at least 0.2mm width of lines cleanly.
The rastercarve author recommends 30 degree engraving bits. But on aluminum, to be safe, I searched 45-60 degree tools. Also, the usual engraving bit shape, like a half cut cone, looked too fragile. More sturdy looking ones (if any) would be better.
I found out most drills, spot drills or other special drills, for metal, have big chisels or obtuse initial angles. In general, tool makers tend to boast complex tool tip shapes, which makes the tools tougher. I tried those first, but I couldn't get to less than about 0.4mm minimum width. (This was actually somewhat fine, but the effects got more cartoonish.)
I tried a 45 degree V bit, Amana Tools #45613 next. But I damaged the tool tip, in a few minutes of test cutting. I had measured the tool length offset as usual, using the auto tool setter installed in the industrial machine. Since the tip radius is near zero, it may not have been good.
I ended up with a 90 degree drill, Nicecut Pinko (English PDF), which turned out fine. But the 90 degree angle may not be ideal for the cut effect (... But actually, the wider the angle, the easier to paint).
On the other hand, the maker says Pinko can cut 0.01mm chamfer, which I have no use for. I want rather, say, clean and reliable 0.1mm cut guarantee.